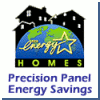
|
 |
Energy Payback
"If you are not using SIPs as your core building material you are not serious about energy efficiency."
Michael Morley, Builder & Author - "Building with Structural Insulated Panels"
There are five reasons foam-panel homes should have lower heating and cooling bills than homes insulated with common wall and ceiling insulation materials:
Structural Insulated Panels achieve thermal ratings of between R-4 and R-7 per inch; batt and loose-fill materials are about half that. -
With less wood, panels reduce thermal bridging (the transfer of heat into or out of a structure through a solid piece of lumber). A 16-foot SIP wall section with one 3 x 4-foot window contains 5 percent wood and 95 percent Insulation. The same wall framed with 2 x 4s 16 o.c. has 20 percent wood and a variable amount of insulation.
If not installed properly, batt insulation is susceptible to voids. Batts are either jammed into narrow cavities, improperly split around wiring or around electrical boxes, or cut too short or too long. In some remodeling jobs, insulation is removed, but not replaced. When used with a trussed roof system, batts won't cover up the bottom chords, allowing heat to transfer directly from the interior of the house into the attic area in the winter and from the attic into the house in the summer. A solid foam panel eliminates these problems.
Any air moving within a conventionally insulated wall or ceiling decreases the energy performance of batt insulation. When properly sealed, foam panels do not allow air movement.
Depending on proper installation and effective sealing of joints and openings, Structural Insulated Panel (SIP) construction lends itself to tighter-than-average construction. This is especially true when SIPs are used for both walls and ceiling because the systems are engineered to connect to each other easily and tightly.
Energy Tables
R Value
|
Panel Thickness
|
Weight (PSF)
|
16.87
|
4.50"
|
3.31
|
25.60
|
6.50"
|
3.47
|
33.20
|
8.25"
|
3.61
|
41.90
|
10.25"
|
3.78
|
50.60
|
12.25"
|
3.95
|
CASE STUDY 1
Place: Watertown, S.D.
Heating degree days: 9,000
Size of home: 1,040
square feet with a full basement, identical floor plans
Energy source: Natural gas, forced-air furnace
|
|
Conventional frame
|
Panel frame
|
|
Walls
|
6' fiberglass batts with 1" foil sheathing; R-24
|
5"EPS-core panels, R-24
|
|
Ceiling
|
12" fiberglass; R-38
|
71/2" EPS-core panels, R-32
|
|
Heated
area
|
Main floor
|
Main floor and basement
|
|
Heating bill
Jan.-March
|
$263
|
$85
|
|
Source: Enercept, Inc., Watertown, SD
|
|
CASE STUDY 2
Place: El Jebel, Colo.
Heating degree days: 7,635
Size of home: 1,336 square feet
Heating source: Electric baseboard; HRV
|
|
Conventional 2 x 6 frame
|
Panel frame
|
|
Walls
|
51/2" fiberglass batts plus 1/2"exterior Insulated, R-22
with airtight drywall (5/8")
|
R-22
|
|
Ceiling
|
Fiberglass batts, R-38 (R-30 in slope)
|
R-38
|
|
Heated area
|
Whole House
|
Whole House
|
|
Heating bill
Oct.-Dec.
|
$450
|
$112
|
|
Source: Big Horn Construction Services, Carbondale, Colo.
|
|
CASE STUDY 3
Place: Ludlow, Mass
Heating degree days: 5,600
Size of home: 2400 square feet
Heating source: Electric
|
|
Conventional 2 x 6 frame
|
Panel frame
|
|
Walls
|
51/2" fiberglass
batts, R-19
|
R-25
|
|
Ceiling
|
9"Fiberglass batts, R-30
|
R-33
|
|
Heated area
|
Whole House
|
Whole House
|
|
Heating bill
Oct.-Dec.
|
$131/mo
|
$30/mo
|
|
Source: Waverly Heights Development Corporation, Ludlow, Mass.
|
|
The walls of this Idaho State Liquor Store in Nampa, Idaho
(pictured above the tables) are 6.5" thick (R 25.6) and 9' high. Most panels measured 8' wide x 9' high.
The total square footage of this building is 2,990 square feet and the walls
were installed in one day. The General Contractor on this project was Sage Construction
of Caldwell, Idaho.
According to the Idaho State Liquor Dispensory, the building saves
them operating expenses every month. There is a similar building located approximately 10 miles away in Caldwell,
Idaho that has a total of 3,010 square feet and was framed using 2 x 6 studs
at 16" on center. Below is the comparative energy costs for the (2) buildings during the winter
of 1997 / 1998:
|
Building 1
|
Building 2
|
2 x 6 Stick Frame 6.5" Precision Panel
|
December 1997
|
$158.92
|
$38.45
|
January 1998
|
$176.46
|
$64.85
|
February 1998
|
$112.85
|
$29.36
|
March 1998
|
$72.81
|
$22.07
|
Totals
|
$521.04
|
$154.73
|
Savings over a 4 month period = $366.31
|
|
|
|